二十余年破碎设备老厂家经验谈:如何提高破碎筛分设备的生产能力
作为二十余年破碎机设备生产的老厂家,今天富康机械带大家来了解下如何提高破碎筛分设备的生产能力?
破碎机的生产能力与待破物料的物理性质(矿石可碎性、密度、解理、湿度、粒度组成等)、破碎机结构参数及工艺要求(破碎比、开路和闭路工作)、负荷率、给矿均匀性有关。
实际生产中,在矿石物理性质、原矿和破碎产品粒度不变的情况下,主要与破碎机排矿口尺寸、破碎比和筛分作业有关,通过调整这些数据,改进设备,可以提高破碎机的生产能力和设备的利用率。
1、选择破碎筛分设备合适的排矿口尺寸和破碎比
1.1 排矿口尺寸
在破碎机排矿口尺寸的调节范围内,破碎机均能正常工作,但根据待破碎物料的特性,每种破碎机通常在中间都有一个最佳的排矿口宽度,在此排矿口宽度下工作,可获得更高的破碎效率,并能延长破碎机的寿命。
以颚式破碎机+圆锥式破碎机组成的二段破碎系统为例:
(1)颚式破碎机排矿口尺寸的选择:例如,颚式破碎机(PEJ900×1200)的排矿口调整范围是150-180mm,实际选择e1=160mm。
(2)弹簧圆锥破碎机排矿口尺寸的选择:例如,PYZ2200中型弹簧圆锥破碎机的排矿口调整范围是10-30mm实际选择e2=20mm。其最大给矿粒度为230mm,颚破产品最大粒度d大=200mm,小于圆锥破碎机的最大给矿粒度,因此两种破碎设备排矿口的选择是符合理论要求的。
1.2 破碎比
总破碎比取决于原矿最大粒度与破碎最终产品粒度,它是破碎筛分设备决定破碎流程的主要指标。例如,根据设计与实际可知,原矿最大给矿粒度D大=650mm,破碎最终产品粒度为d大=25mm,总破碎比S=D大/d大=26。
(1)颚式破碎机的破碎比S1:颚式破碎机产品最大粒度为d大=200mm,其第一段破碎比为S1=3.25。其破碎比范围符合3-6的理论要求。
(2)弹簧圆锥破碎机的破碎比S2:S2=200/25=8,也在破碎比理论范围之内。
2、破碎筛分系统改造
2.1 破碎筛分流程
通过理论计算,各破碎筛分设备在调整排矿口和破碎比之后,其计算的处理能力都符合各设备的理论处理能力。将该二级破碎筛分流程调整后见图1:
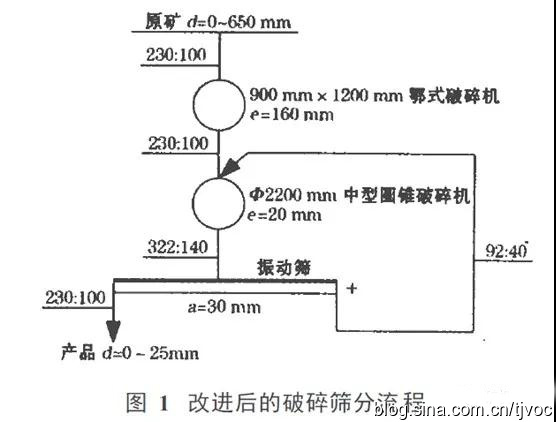
2.2 筛分设备的改进
筛分机的生产能力主要与筛孔的大小和筛分效率有关。筛孔愈大,筛分效率愈低,振动筛的生产能力愈大。在筛分过程中,各种粒级通过筛孔的过程是不相同的,愈接近筛孔尺寸的粒级愈难筛下,因此可以用增大筛孔尺寸的办法,提高振动筛的生产能力,这时虽然筛下产物的大粒度略有增加,但筛下产物的细粒含量也略有增加,筛下产物的平均粒度将不会改变。
为了提高振动筛的作业率,尽量降低筛上产物的循环量,减轻返矿皮带的负荷。鉴于上述经验,实际生产中对筛分设备作出如下改进:
(1)采用自编筛孔尺寸30mm的方形孔筛底,(此尺寸由a=1.2d大得到)。
(2)将筛箱角度略加调整为18°~19°。
(3)对下矿漏斗进行改造,使两台振动筛的给矿量基本一致,达到给矿均匀,下矿角度适宜。
2.3 各种指标比较
上述颚式破碎机+圆锥式破碎机系统改造前后的综合指标见表1:
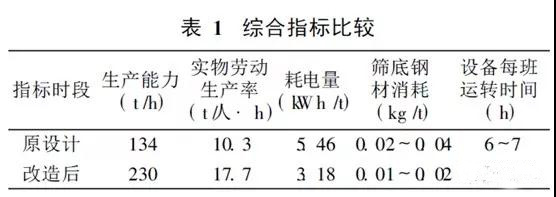
破碎筛分设备生产能力的提高,不仅缩短了工人的工作时间,提高了劳动生产率,而且大大节约了成本,年减少电费42.8万元,降低筛底钢材消耗费用1.5万元,其它间接费用,如油料、备品备件、其它材料和下段磨矿作业成本也相应降低,符合“多破少磨”的原则。
结束语:
(1)实际生产中,在两段一闭路工艺流程条件下,按照所选定破碎设备排矿口进行调整,不仅提高了破碎机的生产能力,保证了破碎产品粒度符合要求,而且小时最高处理能力可达到250t,几乎是原设计能力的2倍,满足了企业扩大再生产的要求。
(2)由于破碎筛分设备生产能力的提高,工人的劳动强度大大降低,节约了电耗和钢材消耗,并缩短了工作时间,延长了设备的使用寿命,在很大程度上起到了提产降耗的作用。
(3)通过对筛分设备部分操作因素和筛箱角度进行调整,既提高了筛分设备的生产能力和作业率,又使矿石在筛面上均匀分布,作低振幅、高振次的运动,解决了筛子利用率低和筛子碰帮的问题,达到筛下产物平均粒度符合要求,筛上产物又不造成返矿皮带过负荷。
(4)破碎工作制度现仍为两班制,但每班工作时间都比原来低2h,这样既可以保证索道运输所需的供矿量,又为职工提供了较为合理的休息和作业时间。